We wanted a gate to exclude mutts from the basement but it's a an awkward location for a hinge and latch. I opted for a slider that would fit into a receiver on the wall, and pass through the existing banister with padded felt. The latch here is just some L hooks and matching pins in the receiver. I swapped this out for mating neodymium magnets. It's all half-lapped pine, very light and strong, with Zinser amber shellac.
Saturday, November 14, 2020
Tensigrity Toy
This was a quick gift for a young science person. I had some fine, braided, polyester cord with zero stretch which is important here. Some finger joints and half-laps add some rigidity.
Table saw sled.
I like using tree branches for a fun, grippy handle. Using a different visual and tactile material is also good UI language to say, "It's okay to touch here, be careful elsewhere."
Sunday, November 28, 2010
A Jig for Mitering Crown Molding
I just tried the "upside down and backwards" method of mitering inside crown molding corners. It worked out fine without a compound miter saw. Search around the net for many more links on this method.
My problem was how to make a series of cuts that line up perfectly when mated in an 12' stick of molding while holding it at an angle against the box wall with one hand. It felt guaranteed to walk around and wreck the run.
I'm no expert, in fact this was my first time, but here's what I learned in case it helps someone. YMMV.
Use MDF crown molding, not pine. It's flexible and cuts very cleanly without splintering. This helped make a sharp joint. See in the sample below, a quick smear of caulk and paint and it disappeared.
Use a jig. I built a physical jig to hold the work for the miter saw. I used a $20 Jorgensen miter box, which turned out to be very decent for general use. Here's what it looked like before I messed with it (that page was also complimentary about the same model). The box has a mounting flange, which I bolted to some scrap wood to let it be clamped in a portable bench vise. Then I screwed some 1/8" plywood to the back and bottom, right into the plastic of the box, countersinking the screws. Next, I made two 45-degree cuts to clear out the plywood where the saw would normally cut. Finally, I held a scrap of crown carefully at the angle it would rest on the ceiling (remember, upside down and backwards) so the back and bottom were seated well to the base all around, and ran a line of finish nails through the wood and down into the plastic. This line of nails helps holds the work firmly, so it can be cut with one hand while holding with the other. Some boxes have a row of holes for dogs for this same purpose.
Use a sample joint as a template. I tested the box a few times, cutting joints and creating a mental jig to remember which end was which and marking the "good" ends L and R, and the "bad" ends X. The test fit looked decent.
Caulk and paint are your friends. Joints won't be perfect. Walls won't be straight, square and plumb. By the way, the molding came primed. I painted it once on the floor before cutting, then after it was finished and caulked, to hide the nail holes and joints.
Be prepared for weirdness. This ceiling was so low, it left no room near the door frame. A "return", or end cap, was the simple answer. This is cut just like an outside corner, with a square end to the wall.
My problem was how to make a series of cuts that line up perfectly when mated in an 12' stick of molding while holding it at an angle against the box wall with one hand. It felt guaranteed to walk around and wreck the run.
I'm no expert, in fact this was my first time, but here's what I learned in case it helps someone. YMMV.
Use MDF crown molding, not pine. It's flexible and cuts very cleanly without splintering. This helped make a sharp joint. See in the sample below, a quick smear of caulk and paint and it disappeared.

Use a sample joint as a template. I tested the box a few times, cutting joints and creating a mental jig to remember which end was which and marking the "good" ends L and R, and the "bad" ends X. The test fit looked decent.
Caulk and paint are your friends. Joints won't be perfect. Walls won't be straight, square and plumb. By the way, the molding came primed. I painted it once on the floor before cutting, then after it was finished and caulked, to hide the nail holes and joints.
Be prepared for weirdness. This ceiling was so low, it left no room near the door frame. A "return", or end cap, was the simple answer. This is cut just like an outside corner, with a square end to the wall.
Saturday, January 13, 2007
Bench Hook
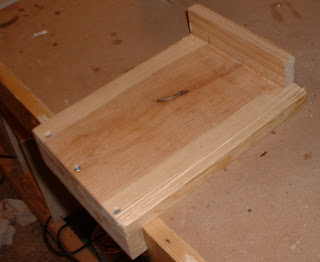
A bench hook might not seem like much, but it's very useful for quick cuts with a hand saw. I've been using it much more frequently since that I've learned how to put a wicked sharp edge onto a chisel: instead of hand holding (ouch) or clamping the work piece, I can set it against the bench hook's fence as something to press against.
Whiteboard Desk

My first major project was a work table with a whiteboard top. This is the project that taught my why traditional furniture uses hardwood post and panel construction instead of a skeleton and skin approach: the result turned out sturdy, light, and good looking but it was a lot of work.
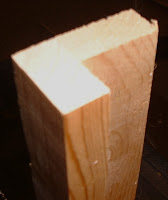
The skeleton is the unusual part. Its members each consist of two pine 1x2's glued at right angles along their length, kind of like an extruded angle beam if this were metal. They form the legs, a top frame, and some cross bracing. The legs, which you can see above, I tapered at the bottom and stained ebony.
A covering of 1/4" birch plywood went on top of the skeleton, with 3/4 round oak molding on all the seams. A learned note here is that it's very hard to make a presentable seam with this plywood, at least with the circular saw blade I used, thus the moldings. They improve its look anyway.
The top is 3/4" MDF with 1/4" whiteboard material glued on top and half-round oak molding around the edges, flush with the top of the whiteboard.
Welcome to the Basement
Join an amateur wood worker as he rediscovers lost methods--many probably lost for a reason--to make things out of wood. The emphasis is currently on making useful projects for the workshop and the home without a full-up woodshop full of specialized tools.
Thanks for reading.
Thanks for reading.
Subscribe to:
Posts (Atom)